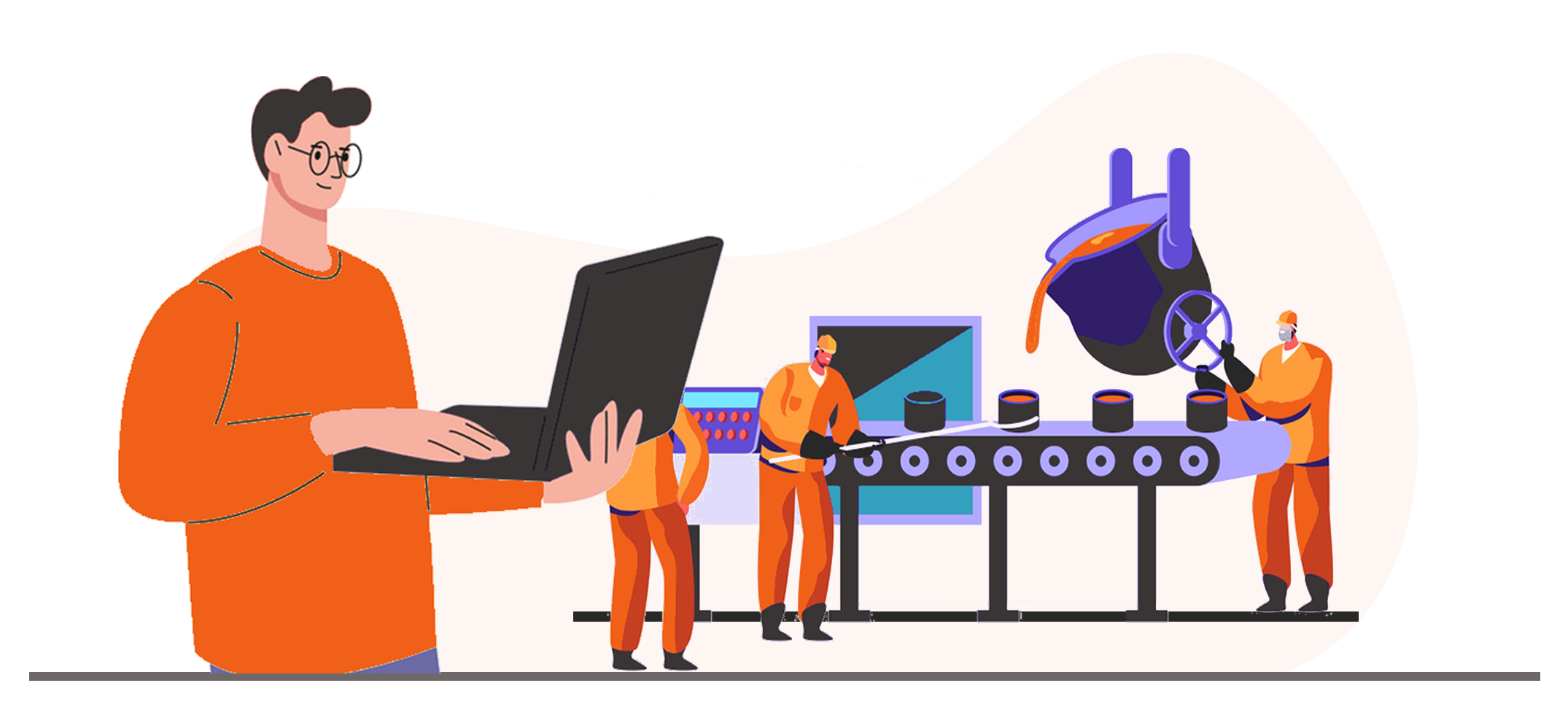
Challenges for plant managers and manufacturing downtime costs
Maintenance is a crucial aspect of any manufacturing plant. Equipment breakdowns and failures can cause unplanned downtime, reduce production, and impact profitability. As a result, plant managers are under pressure to ensure their equipment is always in optimal condition. However, there are several challenges they face in achieving this goal. In this article, we'll explore some of the key maintenance challenges that plant managers are facing and the cost of downtime in manufacturing.
Maintenance Challenges for Plant Managers
Lack of visibility and control over maintenance processes
Plant managers are struggling to gain visibility and control over maintenance processes due to limited resources, outdated technology, and lack of real-time data. This results in reactive maintenance and equipment breakdowns, leading to unplanned downtime and lost productivity.
Maintenance data management
Maintenance data management is a critical challenge for plant managers, as they must manage large amounts of data from various sources, including manual records, spreadsheets, and computerized maintenance management systems (CMMS). This data must be properly analyzed to identify trends and predict potential failures, but the manual process can be time-consuming and prone to errors.
Skilled labor shortage
There is a growing shortage of skilled maintenance workers in the manufacturing industry. This makes it challenging for plant managers to find the right talent to keep equipment running smoothly. As a result, it's common for plant managers to resort to reactive maintenance or outsourcing maintenance work, which can be costly and lead to longer downtime.
Aging infrastructure
The majority of manufacturing plants in operation today were built several decades ago. This aging infrastructure has become more challenging to maintain, leading to increased costs and downtime.
Cost of Downtime in Manufacturing
Downtime in manufacturing can have a significant impact on a plant's profitability. According to a study by the Aberdeen Group, unplanned downtime can cost an average of $260,000 per hour. This includes direct costs such as lost production and labor costs, as well as indirect costs such as customer dissatisfaction and decreased market share.
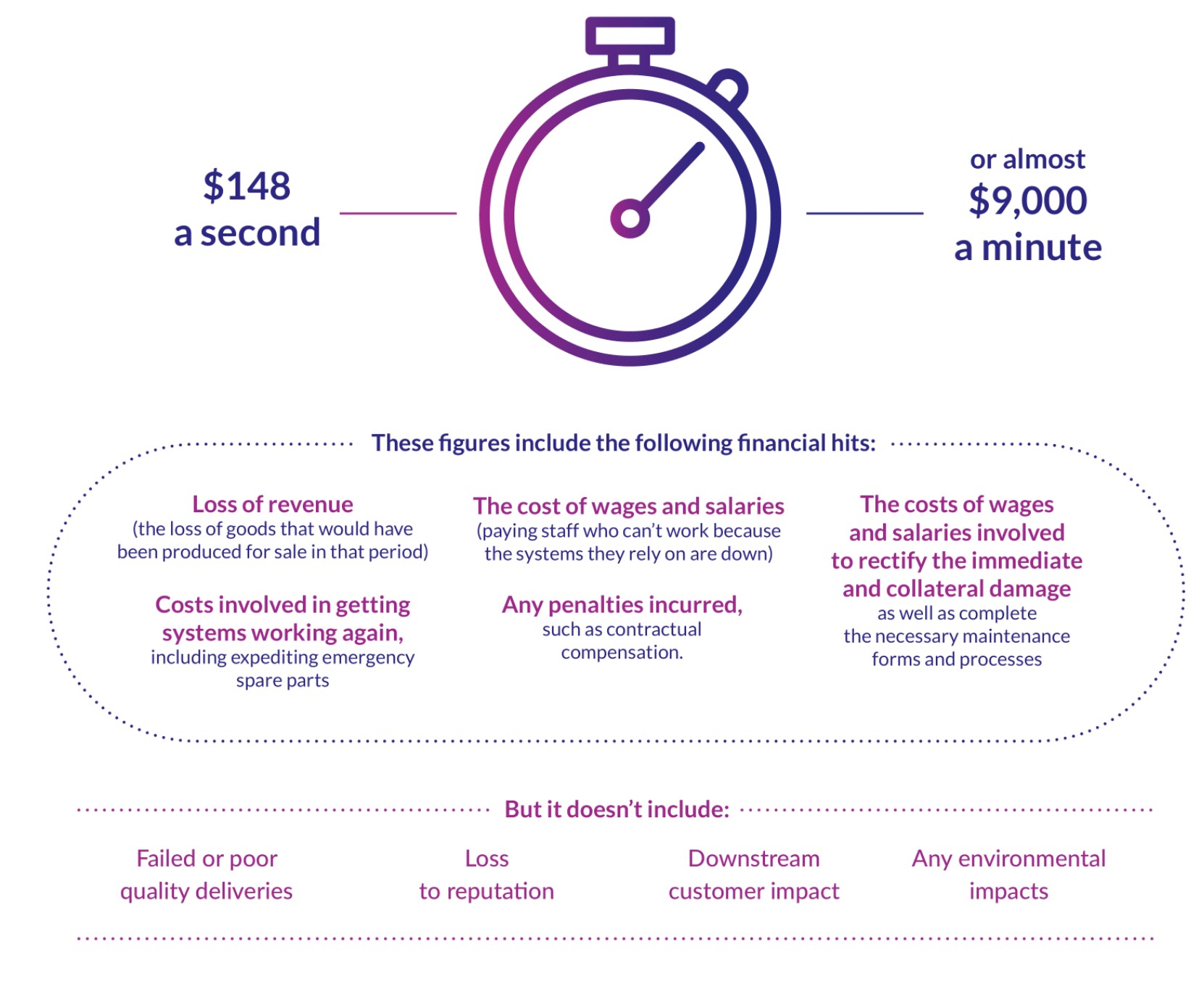
Moreover, the cost of downtime is increasing as the manufacturing industry becomes more reliant on technology. Modern machines and equipment are complex and interconnected, which means that a failure in one part of the system can lead to a chain reaction of failures throughout the plant. This can lead to extended downtime and lost production, resulting in a significant impact on a plant's profitability.
The Solution: Predictive Maintenance
To overcome these challenges and reduce the cost of downtime, plant managers are turning to predictive maintenance. Predictive maintenance uses data analytics, machine learning, and other advanced technologies to predict equipment failures before they happen. This allows plant managers to schedule maintenance proactively, reducing the risk of unplanned downtime. Predictive maintenance provides plant managers with real-time data on the performance of their equipment, allowing them to identify potential issues before they lead to failures. This data can be analyzed using AI and ML algorithms to identify trends and patterns that would be impossible to detect through manual analysis. Based on industry research on Fortune 500 companies , appetite for Predictive maintenance is growing.
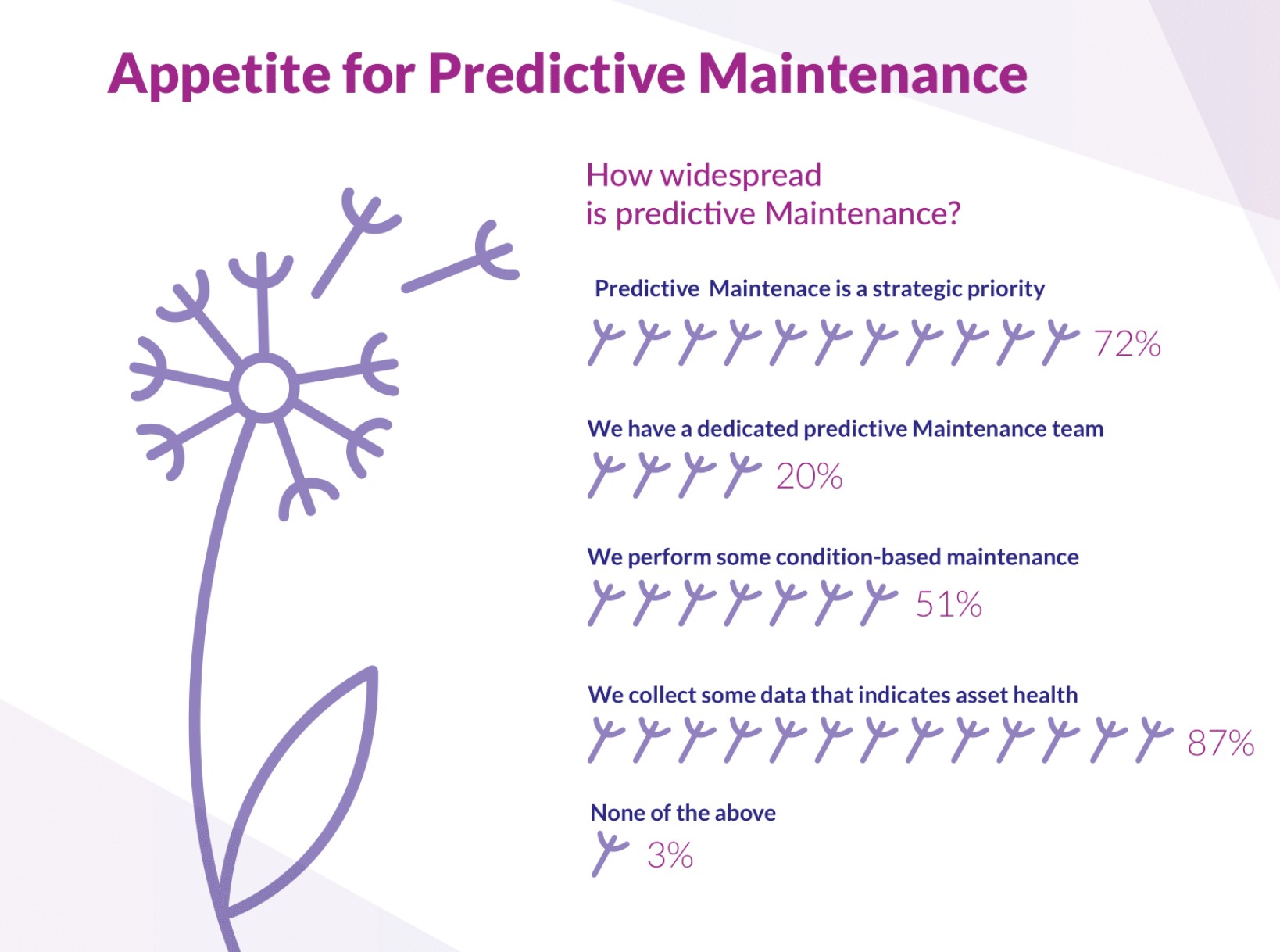
Additionally, predictive maintenance can help plant managers extend the lifespan of their equipment, reducing the need for expensive replacement and repairs. It also ensures that equipment is running at optimal efficiency, reducing energy costs and increasing productivity.
Conclusion
The maintenance challenges that plant managers face are significant, but with the right technology and tools, these challenges can be overcome. Predictive maintenance provides plant managers with real-time data, enabling them to identify potential issues before they result in equipment failure and unplanned downtime. By leveraging predictive maintenance, plant managers can extend the lifespan of their equipment, reduce costs, and increase profitability. It's time for manufacturers to start considering predictive maintenance as a key part of their maintenance strategy to improve uptime and reduce costs.
Are youprepared to handle critical events? Signup for free
If you intersted to follow our blogs : Subscribe